Portfolio
Voor vele projecten heb ik een NDA getekend, daarom kan ik een beperkte hoeveelheid beeldmateriaal tonen, middels storytelling kan ik de (proces)situatie weergeven.
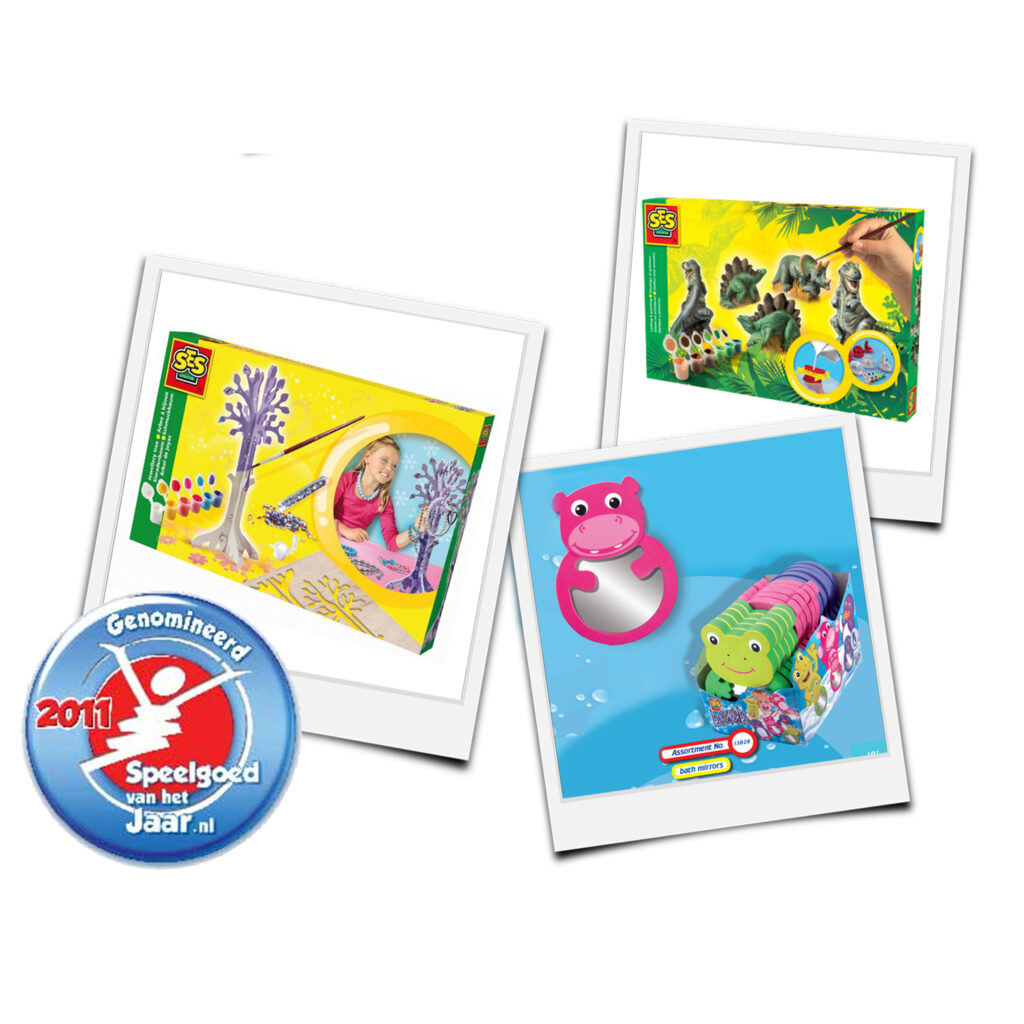
Product & photography
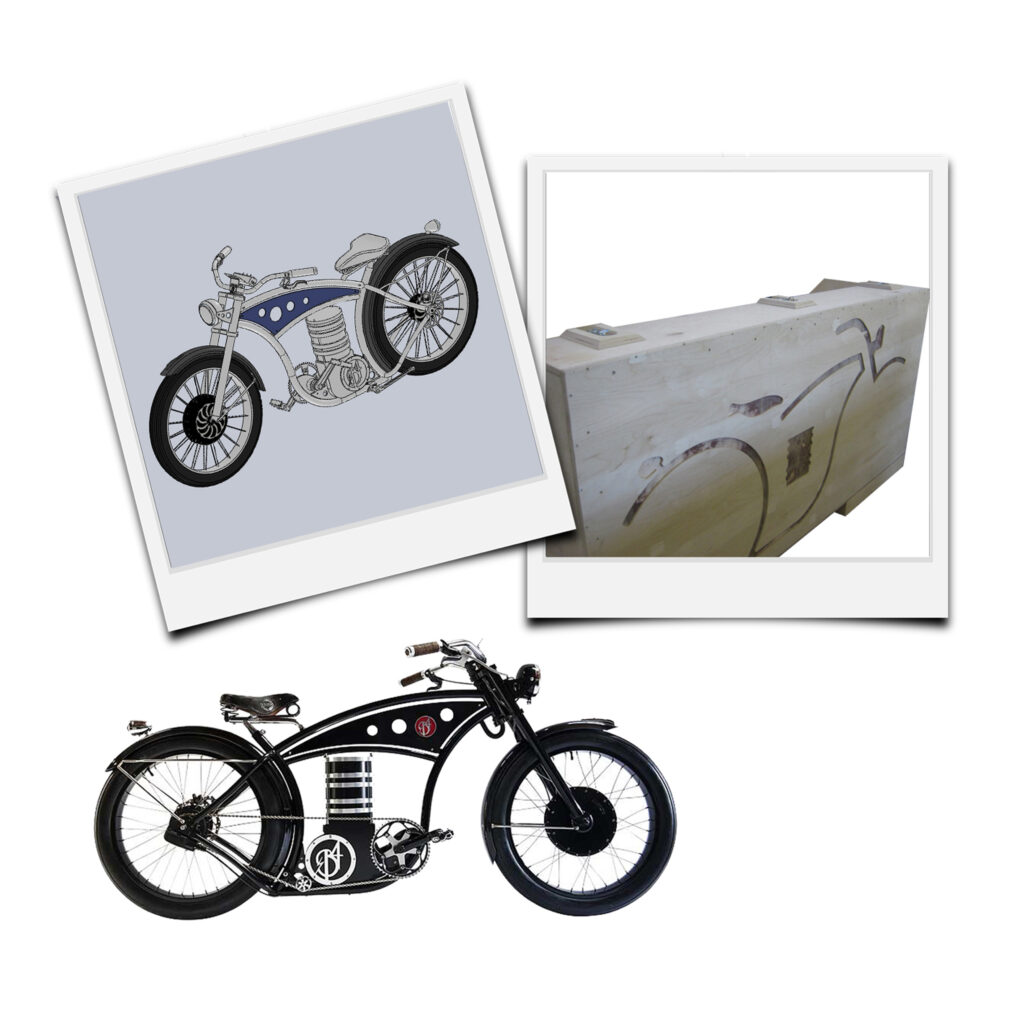
Product & packaging
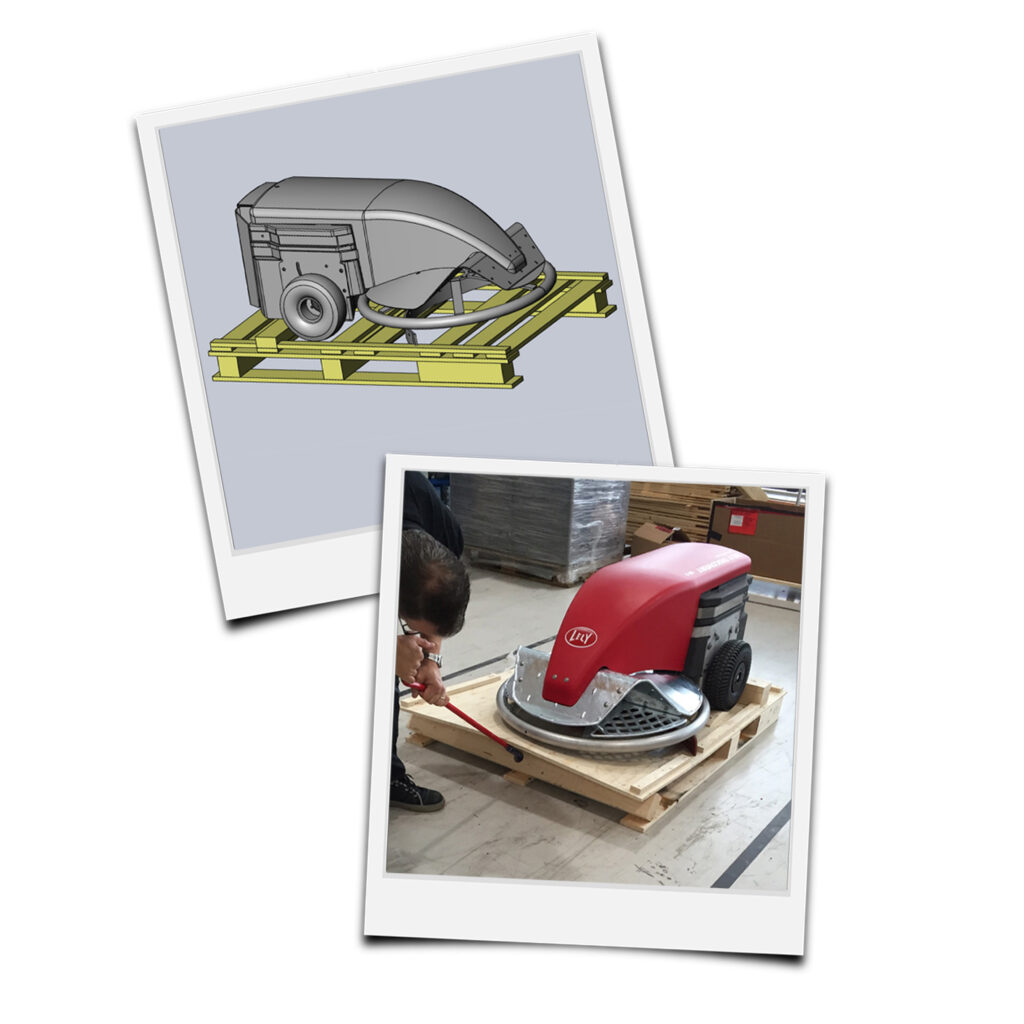
Product & packaging
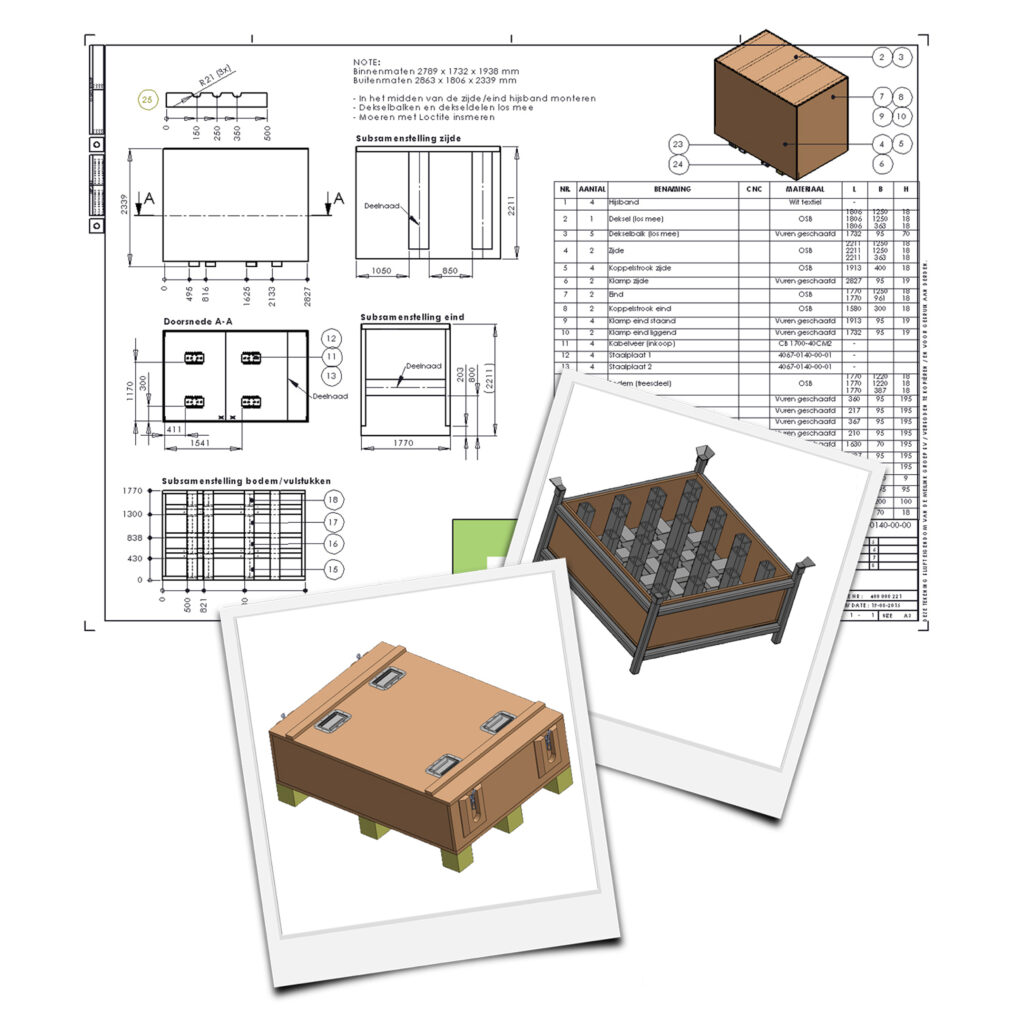
Packaging & tooling
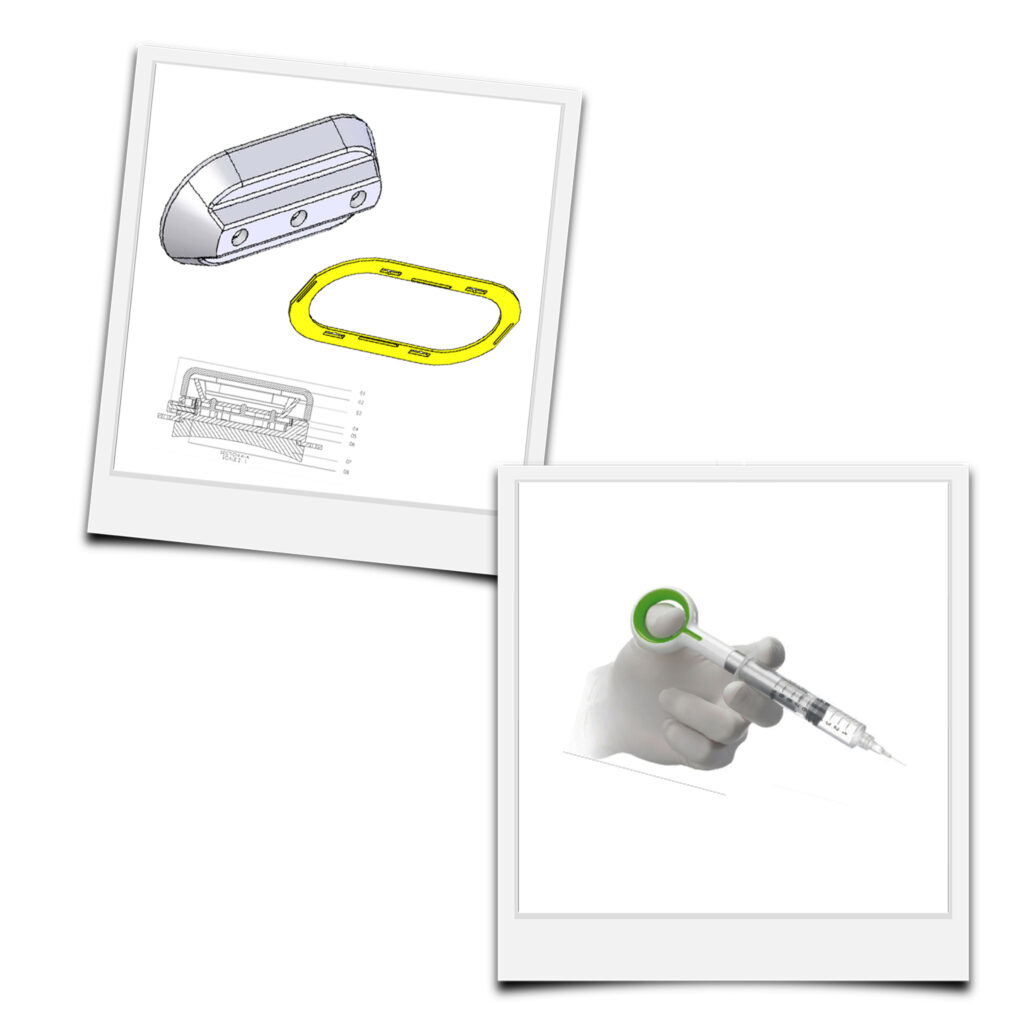
Research & design
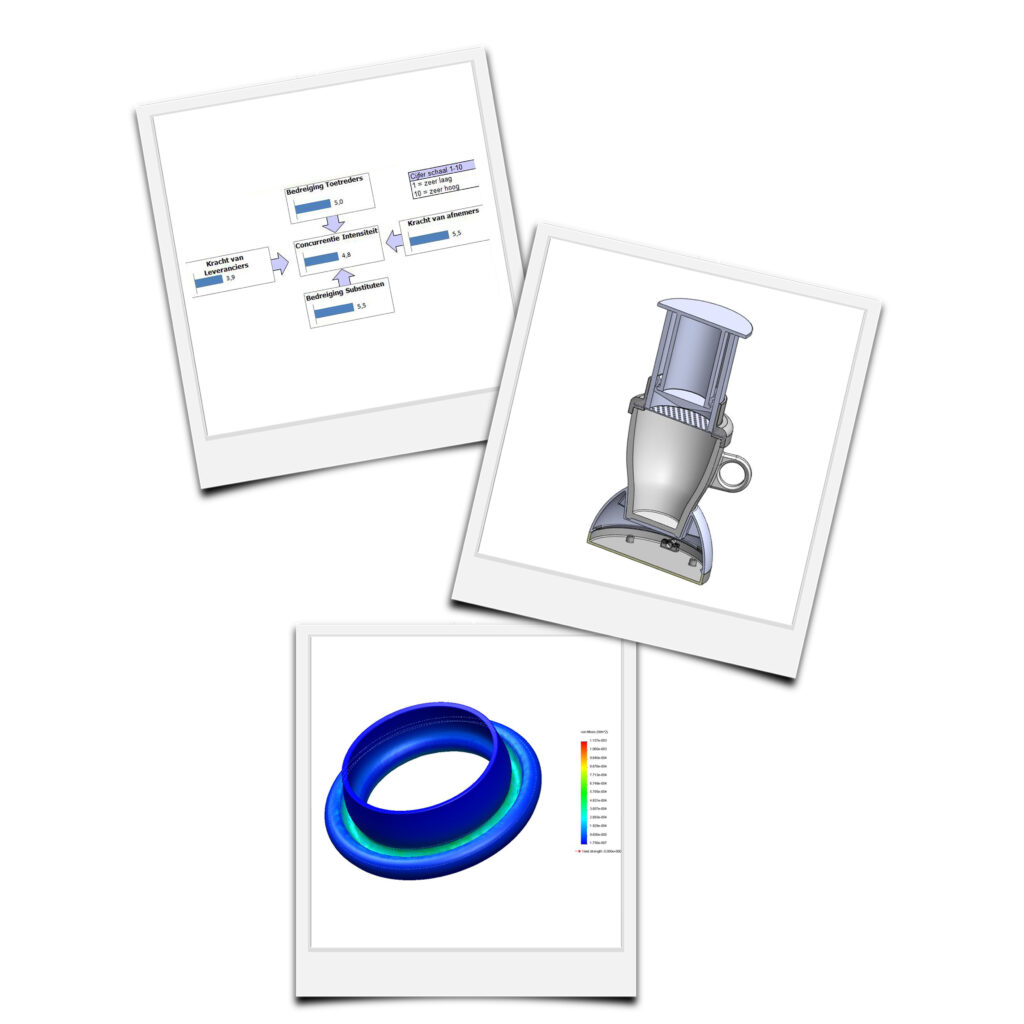
Process & engineering
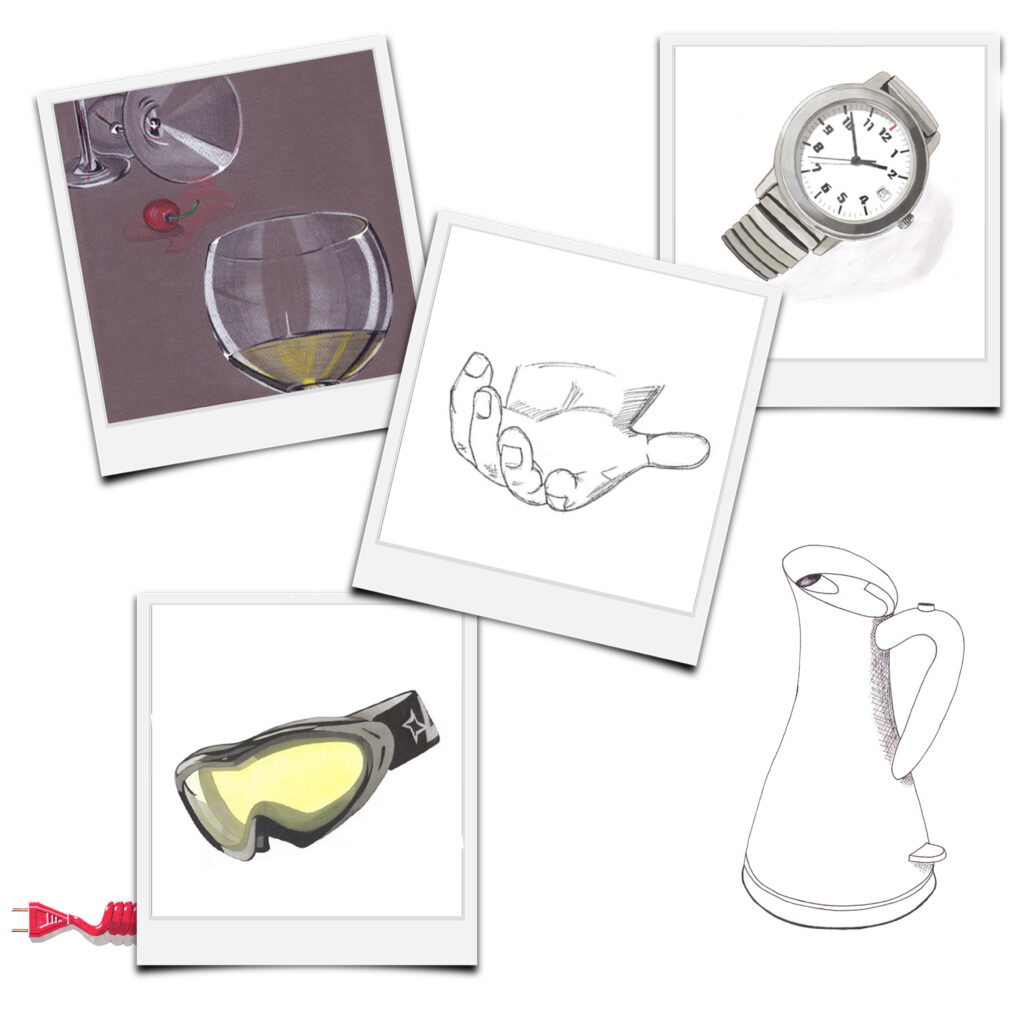
Sketching
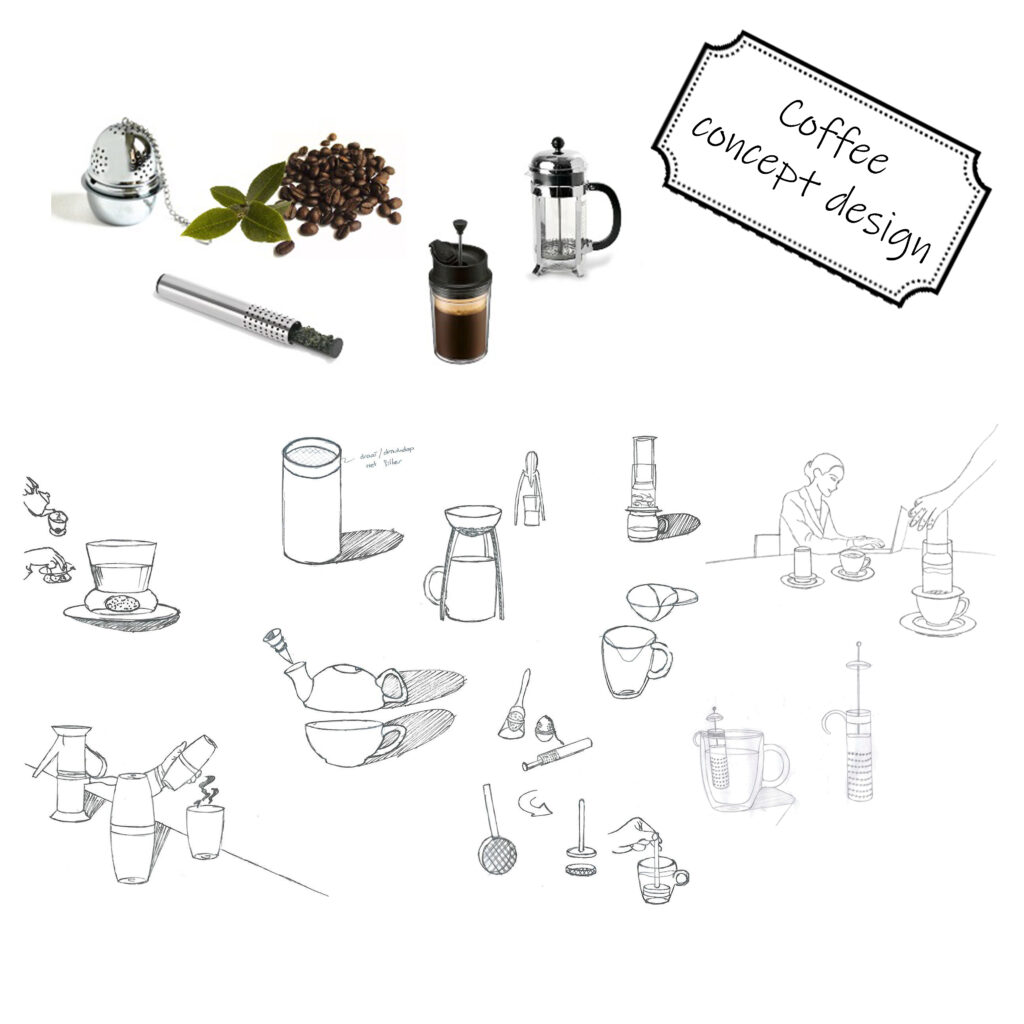
Concept design
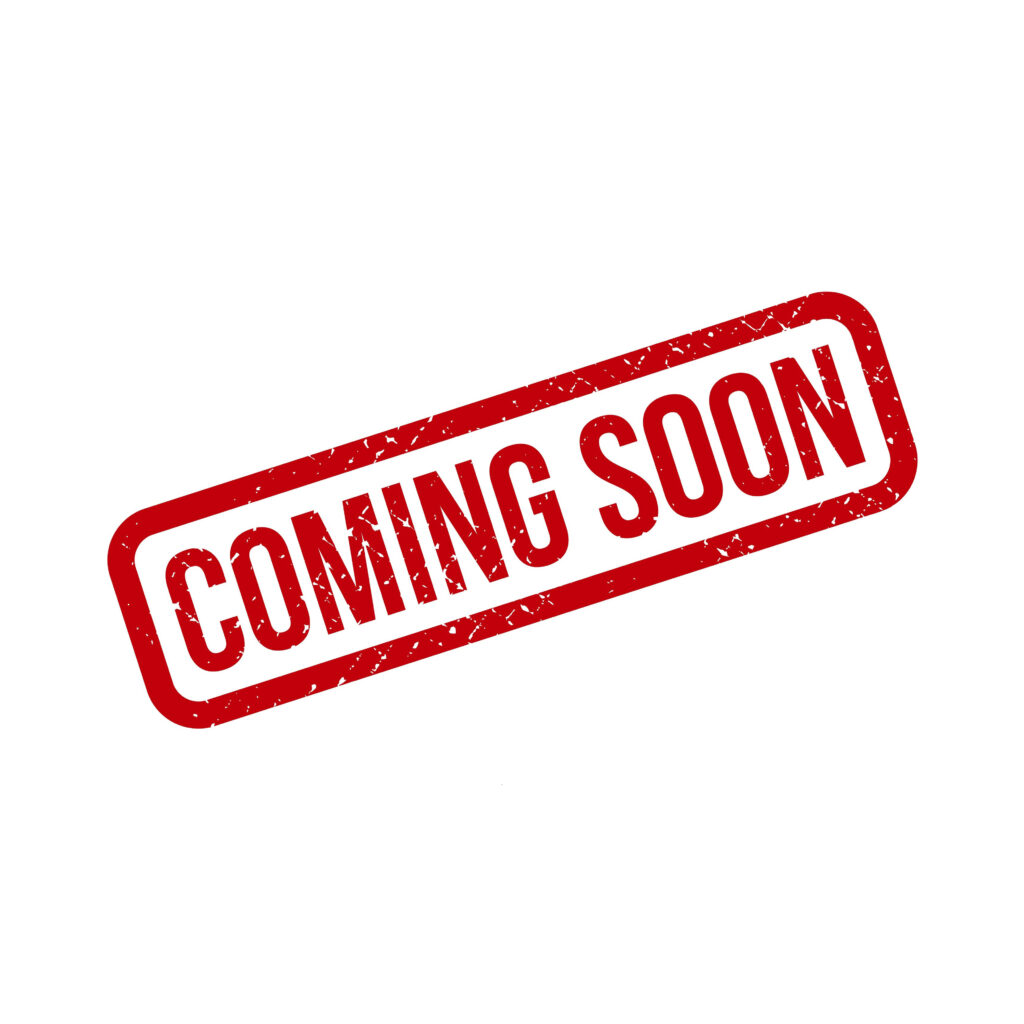
...
Kosten besparen door proces optimalisatie
Herken je dat? Je levert al jaren een product aan een klant en het contract loopt af maar eigenlijk is het niet meer winstgevend in de huidige tijd, wat nu?
Bij deze vraagstelling werd ik enkele jaren geleden betrokken. “Een contract van 20 jaar liep af, moeten we verlengen of niet? Het is een goede klant die we eigenlijk willen behouden maar op deze manier moeten we de komende 20 jaar er geld op toe leggen.” Het betrof een industriële verpakking van een kapitaalgoed.
Allereerst ben ik de huidige verpakking gaan analyseren, tot op detailniveau stelde ik de “waarom” vraag. Van management tot productie had niemand hier een concreet antwoord op, “dat hebben we altijd zo gedaan”. Vervolgens stelde ik aan alle lagen in de keten de vraag “hoe zie jij het voor je en wat zijn jouw wensen?”. Parallel daaraan bekeek ik het huidige proces en het machine park wat voor handen was. Het bleek al snel dat onderdelen nog op de manier van 20 jaar geleden werden geproduceerd, een stuk foam, een mal, een zwarte stift, een handzaag en mankracht. Terwijl er een prachtige snijplotter in de hoek stond te verstoffen, een machine waar flink in geïnvesteerd was maar waarvan men eigenlijk niet wist hoe deze optimaal ingezet kon worden. Ik heb een programma geschreven waarbij de onderdelen genest werden, voor het optimaal benutten van de plaat en voor minder afval. Eén van de wensen was om het stalen onderstel scharnierend te maken zodat er tijdwinst behaald kon worden bij de embaleurs, echter konden we met een berekening aantonen dat dit constructief en financieel niet haalbaar was. Wel kon het frame modulair worden opgebouwd waardoor er logistiek veel verbeterd was en het bij de eindklant gedemonteerd kon worden voor retour zending en hergebruik. Dit is voor mij een circulaire en duurzame oplossing!
Doordat ik me niet alleen beperkt heb tot productontwikkeling maar ook het hele proces en de mensen erbij betrokken heb, hebben we een besparing in tijd, geld en materiaal kunnen realiseren wat uiteindelijk per verpakking op jaarbasis € 300.000,- heeft bespaard.
Met andere woorden mijn advies was om het contract met de klant te verlengen.
Kosten besparen door product optimalisatie
Herken je dat? Problemen bij het spuitgietproces en steeds meer kwaliteitsissues. Kernverschuiving, slijtage en het proces is niet meer beheersbaar. Na vele revisies is het dan toch echt tijd voor een nieuwe matrijs. Al is het nu een flinke investering, uiteindelijk bespaart het tijd, frustratie en afgekeurde producten. Afvalstromen kunnen gereduceerd worden en materialen bespaard. Kwaliteitscontroles kunnen sneller, efficiënter en bovenal het product is strakker en oogt veel beter. Als we voor een besparing gaan laten we dan ook het product optimaliseren en een verbeterslag maken. Waaraan voldoet het product nu en waaraan zou het moeten voldoen. Ik neem als voorbeeld een kunststof bocht voor een riolering. Kan de wanddikte niet dunner? Kan de insteekdiepte of bocht niet korter? Allerlei aspecten die we nu kunnen aanpakken bij het bestellen van een nieuwe matrijs maar kan dat zomaar? Ik ben de normen nagegaan en heb bekeken aan welke kwaliteitseisen het product moet voldoen. Maar bovenal heb ik goed gekeken en geluisterd naar de ervaring van mensen en het gebruik in de praktijk. Dit gaf mij het inzicht in de vormvrijheid maar ook beperkingen van de productontwikkeling. Theorie en praktijk zijn niet vanzelfsprekend gelijk. Ik ben van mening dat je pas echt goede producten kunt ontwikkelen als je weet hoe het geproduceerd wordt en hoe een eindgebruiker ermee werkt. Met andere woorden, ik werk niet alleen vanaf mijn CAD station maar ga ook de werkvloer op en het veld in.
Met dit ontwerp bestaande uit twee varianten uit één matrijs heb ik een materiaal/gewichtsbesparing van 15% gerealiseerd dit maal 326.838 stuks op jaarbasis wat neer komt op een besparing van €93.000,- en realiserende dat het assortiment tientallen producten telt. Na één jaar is de investering in de nieuwe matrijs terugverdiend. De jaren erna is het winst, de levensduur van een matrijs is gemiddeld 30 jaar dus dat rekensommetje is snel gemaakt. Naast de financiële besparing is er ook een tijds- en afval besparing gerealiseerd. Mensen in productie en in het veld werken sneller en prettiger.
Dit is voor mij een voorbeeld van circulair oplossing!
Revisiebeheer, hoe doe je dat?
…. (coming soon)
Nieuwe product innovatie
Herken je dat? Je hebt een idee voor een nieuw product of je ziet bij de concurrent iets wat ook perfect zou aansluiten bij je eigen assortiment maar dan wel graag iets anders en beter. Alleen blijf jezelf continu in hetzelfde cirkeltje denken en zie je vooral veel redenen waarom iets niet zou werken. Laat mij je dan helpen om er met een frisse blik er naar te kijken. Ik parkeer door middel van verschillende brainstormtechnieken of creatieve sessies alle “beren op de weg” en laat alle “ja maar” even los. Ik denk net even anders dan een ander, omdenken, soms heel extreem of totaal niet relevant en dat is nou juist de bedoeling. Op die manier komen de innovatieve ideeën, “goh dat ik daar zelf niet aan heb gedacht”. Vaak zo eenvoudig en voor de hand liggend. Met weinig middelen en investering zijn doelen dan ineens wel te bereiken.
Tegeltjes wijsheid:
“Als je doet wat je deed, krijg je wat je kreeg”